Standardiser votre environnement de travail avec la méthode 5S
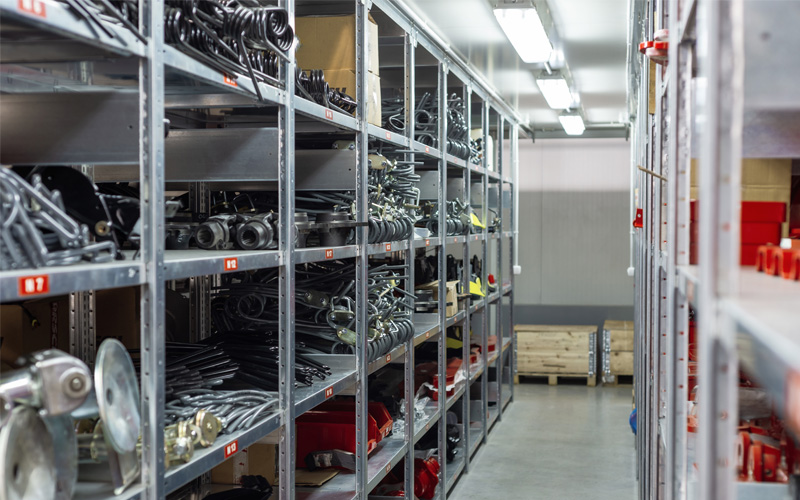
D’où vient la méthode des 5S ?
La méthode des 5S est une méthode d’organisation japonaise conçue et développée par le groupe Toyota afin d’améliorer l’environnement de travail au sein de ses lieux de production.
En quoi consiste la méthode des 5S ?
-
La méthode des 5S est une pratique traduisant la volonté de débarrasser son environnement de vie ou de travail des choses qui l’encombrent, de veiller à ce qu’il reste rangé, de le garder en ordre, de le nettoyer et d’y instaurer la rigueur nécessaire à la qualité et au juste à temps. Elle fonctionne aussi bien pour l’usine que pour le bureau et elle se base sur des règles de bons sens et simples mais qui souvent sont négligées. Pour réussir à mettre en place les 5S, il faut les appliquer dans l’ordre et les mener jusqu’au bout.
-
C’est une démarche qui apporte de nombreux bénéfices et est très bien acceptée par les utilisateurs. Néanmoins, comme elle est très visible et change les manières de travailler de nombreuses personnes, sa mise en oeuvre doit appliquer un processus rigoureux et une excellente communication.
Quels sont les avantages de la méthode 5S ?
-
La méthode 5S profite non seulement aux propriétaires d’entreprises, mais également à leur personnel et à leur clientèle.
-
Son principal avantage réside dans le fait que le lieu de travail est plus propre, plus sûr et mieux organisé. C’est souvent la première étape d’une démarche d’amélioration continue visant à éliminer le gaspillage, ainsi qu’à accroître la productivité et les profits.
-
Faire participer les membres du personnel à l’amélioration des processus peut aussi être bénéfique pour le moral et les conditions de travail. Pour les clients, la méthode 5S peut entraîner une baisse des prix et une amélioration des produits en faisant pression sur les autres entreprises du secteur pour qu’elles en fassent autant.
-
« Pour qu’une entreprise tire pleinement parti des avantages de la méthode 5S, le processus doit être fonctionnel », expliquent certains experts qui ont une vaste expérience en génie industriel. « Certaines entreprises se contentent de faire ce que on appelle les « 5S esthétiques ». Elles procèdent machinalement sans intégrer la méthode à la culture d’entreprise. Or, les 5S doivent faire partie des activités quotidiennes. »
Points forts des 5S au quotidien
-
Amélioration de la sécurité
-
Réduction du gaspillage
-
Baisse des coûts de production
-
Plus grande disponibilité de l’équipement
-
Baisse du taux de perte
-
Amélioration de l’agilité et de la flexibilité de la production
-
Renforcement du moral du personnel
-
Amélioration de la réputation auprès des clients, des fournisseurs, des membres du personnel et des gestionnaires
Que désignent les 5S ?
Les 5S désignent un processus en 5 actions pour améliorer l’environnement de travail. Ce sont 5 verbes d’action résumant les cinq tâches essentielles permettant d’améliorer l’environnement de travail.
Il s’agit de :
-
Seiri (整理) : supprimer l’inutile, débarrasser.
Le premier des 5S, il faut commencer par se débarrasser de ce tout ce qui est inutile. S’il est important de garder, il est également important de jeter. Mais surtout, il faut savoir ce qu’il faut garder et ce qu’il faut jeter.
-
Seiton (整頓) : situer les choses, ranger.
Il s’agit de positionner quelque chose à un endroit précis pour pouvoir le retrouver immédiatement lorsque l’on en aura besoin et sans perdre de temps à le chercher. Il faut positionner les objets en fonction de leur fréquence d’utilisation.
-
Seiso (清掃) : (faire) scintiller, nettoyer.
Le fait de nettoyer des bureaux, des lieux de travail et des moyens de production va bien au-delà de la simple propreté. Pour les machines et l’outillage par exemple, c’est un premier pas vers l’auto-maintenance car c’est c’est lors du nettoyage que l’on détecte les usures prématurées et anomalies.
-
Seiketsu (清潔) : standardiser les règles, maintenir l’ordre.
Lors de cette étape, les règles par lesquelles le lieu de travail restera débarrassé des objets inutiles, rangé, nettoyé sont définies. Le management visuel est préconisé afin d’éliminer les risques de désordre.
-
Shitsuke (躾) : suivre et progresser.
C’est le dernier S, il définit qu’il faut respecter les règles précédemment établies et par là même encourager le personnel à y adhérer. Il convient de toujours faire ce qu’il faut afin que les 5S deviennent une habitude.
Les représentations du 5S
La décision du déploiement de la méthode 5S, nécessite une première approche en mode projet, celle-ci nécessite du temps et des ressources et va modifier les conditions de travail de nombreuses personnes.
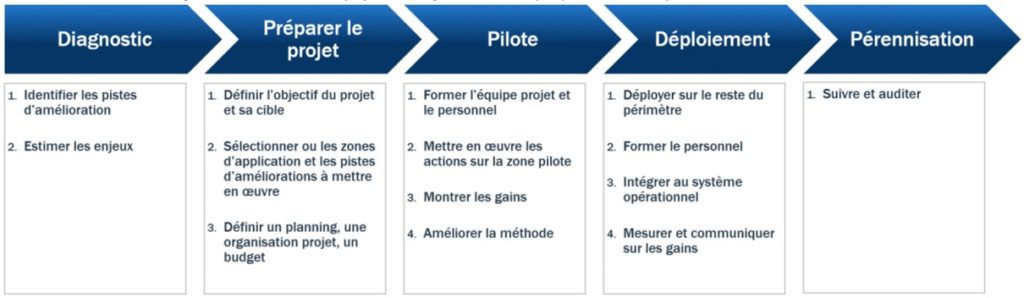
Une fois la méthode déployée et acceptée, on la représente plus couramment en roue, pour que celle-ci soit considérée comme continue, normale et ancrée dans la culture.
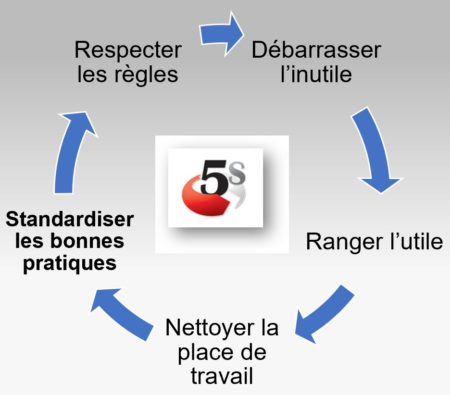
Mon expérience personnelle
Bien souvent la décision du déploiement de la méthode 5S est prise par le management, or pour se faire il faut définir une équipe de terrain, qui doit adhérer et s’approprier le projet.
J’ai régulièrement au début d’un projet 5S rencontré des personnes réticentes, craintives au changement et ayant peur d’une certaine industrialisation des activités.
Mais dans la majorité des cas que j’ai vécu et pour autant que l’on fédère et donne des moyens correspondant aux besoins, ces mêmes personnes qui ont initialement des craintes, s’approprient le projet, le mettent avec plaisir en place et deviennent même parfois les garants du 5S.
ARIAQ vous accompagne dans votre chantier 5S
Planifier votre déploiement, La formation standardiser 5S SMED est déterminante afin de réaliser celui-ci.
Faites-vous accompagner et commencez par identifier les changements. Contactez-nous pour en discuter. Au plaisir d’en parler avec Vous !
Tel central : +41(0)24 423 96 50,
Formation disponible chez ARIAQ : Chef de projet Lean Production
Tonino Placi – Formation et Conseil en Supply Chain
Mécanicien de Machines et Technicien ES en Exploitation & Logistique, Tonino a acquis au cours de son parcours professionnel une grande expérience en gestion de projets industriels, en planification de production et ordonnancement, achats stratégiques et composants mécaniques, et gestion de stock. Passionné par l’amélioration continue il aime rechercher les failles afin de trouver des solutions optimales en tenant compte du terrain et des besoins techniques.