Gagnez en efficacité et en sécurité grâce aux standards de travail
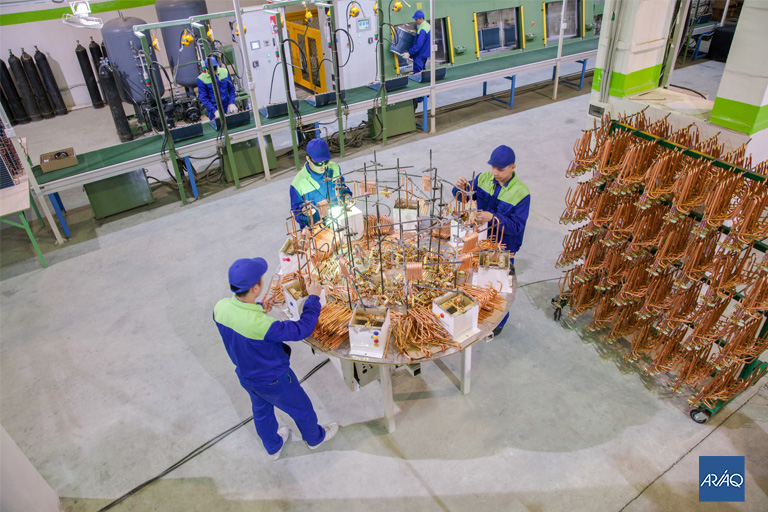
Le standard est la meilleure méthode connue à ce jour, qui est partagée et co-construite par les utilisateurs, pour effectuer une tâche liée à un processus :
-
Fabriquer un produit ou établir un document comptable
-
Utiliser, régler et entretenir une voiture ou une machine ou un équipement de bureau
-
Évacuer un bâtiment
-
Mesurer le délai de production d’un passeport : DEBUT = prise de rendez-vous sur internet => relevé d’empreinte et saisie des données => Production et livraison du document =>FIN = Notification à l’usager que le document est disponible
-
Contrôler une pièce de façon répétable est reproductive
Qu’est-ce que le standard ?
Le standard décrit la séquence des mouvements ou éléments de travail réalisés par chaque personne en vue d’accomplir un cycle de travail, ci-dessous des exemples :
-
Les éléments physiques nécessaires au processus (machines, tables, Poka-Yoké, outils, protections …)
-
Leurs places
-
Leurs paramètres de fonctionnement (consignes de réglages, repères physiques à respecter …)
-
Ergonomie, consignes, règles de sécurité
Il existe des standards pour différents types d’activités :
-
Standard de démarrage
-
Standard de réglages
-
Standard de nettoyage
-
Standard de maintenance : Lubrification, analyse de pannes (troubleshooting), préventive/périodique
-
Standard d’étalonnage, de mesurage, de contrôle…
Comment mettre en œuvre et ancrer les standards ?
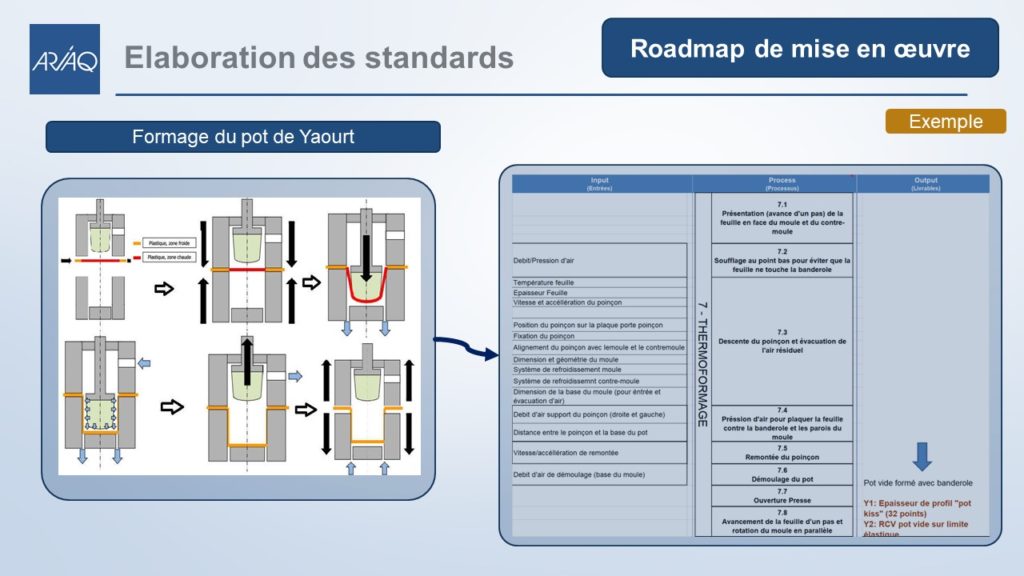
En suivant les étapes ci-dessous, vous serez en mesure de mettre en place des standards efficaces et pragmatiques
1. Décrire de manière exhaustive le processus à l’aide d’un diagramme de flux et en énumérant tous les facteurs influents en utilisant la méthode des 5M (machine, main-d’œuvre, matières premières, méthode et milieu)
2. Faire des essais le cas échéant pour ajuster ou définir des plages de variations.
3. Établir avec les acteurs du processus les seuils d’alerte et les règles de réaction à adopter.
4. Construire le standard : un document, un simple visuel, une solution technique didactique…
5. Tester et former les équipes aux standards
6. Mettre en place une matrice de polyvalence et un plan de formation pour piloter l’ancrage des standards sur le périmètre concerné
En conclusion, les standards se révèlent être des instruments incontournables en vue d’accomplir avec efficacité et de manière homogène les tâches liées à un processus. Ils permettent une description exhaustive des éléments physiques nécessaires à l’opération, de leurs emplacements, des paramètres requis pour leur bon fonctionnement ainsi que des règles de sécurité inhérentes à l’exécution de ladite opération. Diverses catégories de standards sont en outre disponibles, chacune étant destinée à une activité particulière telle que le démarrage, les réglages, le nettoyage, la maintenance, l’étalonnage et le contrôle.
Article rédigé par Hervé Pochart, Consultant Senior en Excellence Opérationnelle
Hervé a développé depuis 20 ans son expertise en occupant successivement des postes opérationnels en amélioration continue dans 2 groupes allemands KSB (pompes et robinetterie industrielle, SGL CARBON (Graphite et fibres de carbone). Toujours aussi curieux de découvrir de nouvelles activités, consultant depuis plus de 12 ans, il pilote dans différents secteurs industriels, services, des plans de transformation des organisations et aime accompagner les équipes en place vers l’excellence opérationnelle.
Certifié MBB LSS depuis 2007 et accrédité formateur IASSC depuis 2016, ses capacités de formateur et de coach lui ont permis de certifier à ce jour plus de 200 Black Belt LSS et 800 Green Belt LSS ainsi que des Master Black Belt.